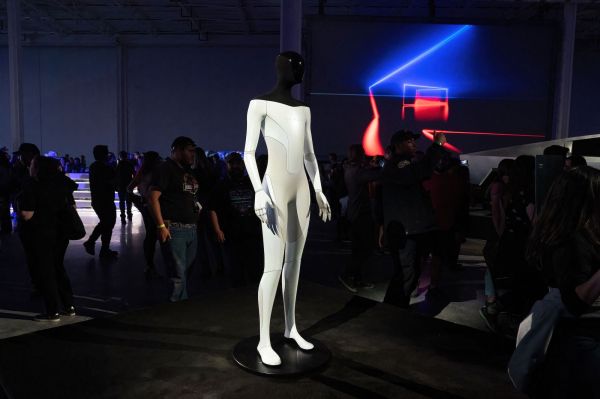
Musk says robot, aimed for 2023, will be worth more than Tesla’s car business
April 22, 2022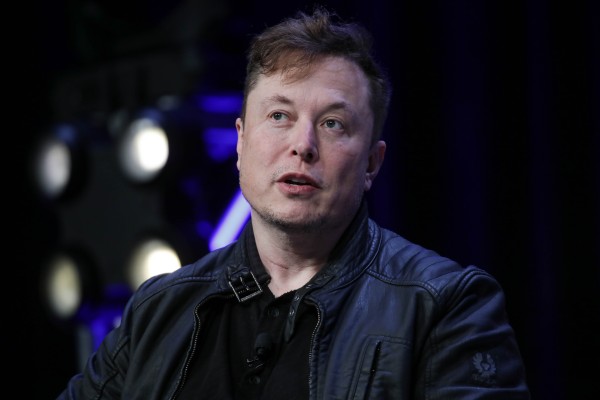
Musk says Tesla aspires to mass produce robotaxis by 2024
April 22, 2022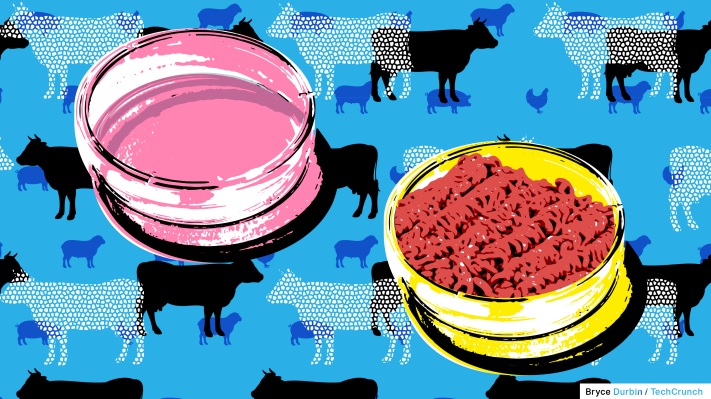
Cultivated meat, grown in a bioreactor rather than out on the range, might be one of the big food trends of the decade. But it’s relying on tech built around multiplying yeast and bacteria cells, not animal tissue — and Unicorn Biotechnologies wants to change that with new equipment created with mass food production in mind. It’s just raised $3.2 million to turn its prototype bioreactor into a commercial product.
Though we hear about new cultivated meat companies and funding rounds with frankly amazing frequency (this one happened while I was writing this!), there are fundamental questions about whether this method of growing meat can scale. The simple fact is that animals like cows are grown in huge environments that are mostly empty or filled with hay; every gram of cultivated meat comes through an expensive, complex machine that probably wasn’t designed to do this stuff in the first place.
“Most biomanufacturing systems were designed and optimized for making bacteria (making enzymes) or yeast (brewing beer) or are focused on making the byproducts of animal cells (vaccines), not the animal cells themselves,” said co-founder and CEO of Unicorn Bio, Jack Reid. “Using this legacy hardware to cultivate meat requires one to reengineer the cells. Our approach and core conviction is that it is actually easier, and ultimately better, to design new hardware systems aimed to foster the growth around the cells, rather than trying to fit these cells to existing engineering systems.”
Of course it’s not like these companies with big money are just buying stuff off the shelf. But the industry is moving fast and critics have pointed out that even the most wildly optimistic figures are paltry compared to the traditional meat industry. If they want to change the world, they’ll need to replace more than 1% of beef.
Unicorn aims to change that with automation and modularity built with scaling in mind from the start.
“Today, one of the biggest challenges for biomanufacturing is bioprocess optimization. It can take years — or even decades — to scale a bioprocess to large-scale bioreactors (imagine steel tanks the size of a small house),” Reid said. Unicorn’s modular approach uses many smaller systems operating in parallel; smaller volumes are easier to control, and also easier to add or subtract to meet demand or replace others.
Reid also claims a higher level of automation for its machines — which, to be clear, are still at prototype stage. But bioreactors were only very recently only found in biotech and pharmaceutical laboratories and aren’t exactly designed for easy operation and customization.
“We’re creating a system that is automated end-to-end. To operate it, you don’t need a Ph.D., you simply need to ‘plug in’ your starting ingredients, select the product you’re growing and let the system take care of the rest,” he said. While there’s almost certainly a little more to it than that, the system will use built-in sensing, machine learning and industrial automation tech to this end. Some of these can already be found in the innovations of other cultivated meat startups, but it’s a fast-moving sector.
Here’s Y Combinator’s answer to cultivated meat’s scaling problem
Ultimately Unicorn doesn’t want to make meat itself but act as an enabler for others in the industry.
While the potential for cultivated meat is massive (to reduce greenhouse gas emissions, animal suffering and to increase food security in our rapidly changing climate), this will only be realized if breakthrough technologies are made available to all of the players establishing this field,” said Reid.
If a company has discovered a great cell line or growth method but isn’t an expert in engineering bioreactors or nutrient flow, they would be able to set up Unicorn hardware as they scale up rather than repurposing tech from a different era.
Reid disagreed with some of the more outspoken critics of the potential of cultivated meat, but said it’s true that with today’s technology (which is to say, yesterday’s) we can’t possibly hit the volumes necessary to make a dent in the ethical and environmental issues fundamental to raising animals for slaughter. Innovation is necessary to make even the smallest impact.

Image Credits: Unicorn Biotechnologies
Image Credits: Unicorn Biotechnologies
The $3.2 million seed round ought to help move Unicorn forward; it was led by Acequia Capital, with participation from SOSV, Marinya Capital, Alumni Ventures, C3, CULT Food Science and others. They’ve already spent some of it to hire up a bit and are looking to provide a proof of concept scale machine capable of producing kilograms of cells by the end of the year. Pilot projects with partners could begin around that time, or in early 2023.
“Although much work remains ahead,” said Reid, “We retain the conviction that sustained innovation at the intersection of biology, engineering and bioprocess automation will continue to unlock tangible technologies to help the cultivated meat ecosystem achieve its full potential.”
UPSIDE Foods bites into $400M round to serve cultivated meat later this year